Robots Relieving Our Workers of Their Workload
Robots Relieving Our Workers of Their Workload
1) First, can we get to know you better? Could you please tell us about your professional background?
Greetings. Of course, my name is Yusuf İleri. I work as the Global Technical Director at Kastamonu Entegre. Having graduated as a bachelor from the Department of Forest Industrial Engineering at the Faculty of Forestry of Karadeniz Technical University and from the Faculty of Business Administration of Anadolu University, I completed my Master's Degree in Business Administration at Gebze Technical University.
For 34 years, I have been working on production management, optimization, efficiency management, product, process and technology development in the wood-based panel manufacturing industry. Currently, I am working on digital transformation, renewable energy production and energy efficiency initiatives as part of industry 4.0. I undertake initiatives to enhance our competitiveness and to develop an environmentally sensitive production approach.
2) We kindly ask that you explain your company's organizational structure and recent business agenda.
(establishment, location, indoor-outdoor areas, product line, production capacity, plant(s), headcount, industry engaged in, areas of expertise, exports, etc.)
We have 56 years of experience in the wood-based panel industry. We manufacture MDF, particleboards, laminate flooring, door skins and value-added products to cater for the demand in furniture, decoration and construction industries.
We have production facilities in Kastamonu, Gebze, Balıkesir, Samsun and Adana domestically and in Romania, Bulgaria, Bosnia and Herzegovina, Russia and Italy globally, in a total of 6 countries. We are the industry leader in Turkey thanks to our annual production capacity of 7.8 million cubic meters Additionally, we are the third largest MDF and particleboard manufacturer in Europe and the fourth largest in the world.
Our products are delivered to millions of users in 100 countries on 6 continents. We have a significant market share and competitiveness in the countries where our production facilities are based. We have a strong presence in these markets, holding 35% of the market share in Bulgaria, 30% in Russia and 30% in Romania. In addition, we are one of the largest Turkish investors in Italy and the largest MDF producer in Russia.
At Kastamonu Entegre, we employ 7000 people from 13 different nationalities in domestic and overseas production facilities and offices, leveraging our strength and experience in production.
3) Could you please share your new investment (line, facility investment, efficiency, capacity - quality improvement) plans and goals for 2025, considering 2024?
I can say that we have come out of a period of focusing on domestic investment. The two ‘mega-site’ production facilities we commissioned in Balıkesir and Kastamonu played a key role in increasing our production capacity and competitiveness in Turkey. With our new production line launched in the particleboard plant in Pomposa of Italy, we also enhanced our production volume in Italy by increasing our total investment to 250 million Euros. Additionally, these investments helped strengthen trade relationships between the two countries by increasing exports and employment.
Investing in renewable energy resources, we did not only save energy but also developed eco-friendly production processes. Our biomass and solar power plants produced enough clean renewable energy to power 100,000 homes for a year.
While pioneering in the industry thanks to our sustainability- and innovation-driven solutions, we greatly contribute to the circular economy through our environmentally friendly products such as 100% bio-based Pureboard. Additionally, we make a difference with our green innovations such as wood-based panels made by upcycling coffee waste and using recycled materials.
In 2025, we intend to focus on the effective use of our available production capacity and further increase our productivity. We plan to prioritize projects that will reinforce our position in current markets and enhance our competitiveness. In this respect, we will focus on developing sustainability-oriented projects, working on innovative products and investing in creating more value for our customers.
In addition, we will continue to take initiatives with focus on energy efficiency by expanding the use of renewable energy resources. Our investments in digitalization, product development and sustainability will enable us to keep reinforcing our leadership in the industry and create a lasting value in all markets where we are present.
4) What are the pros and cons of producing Building Materials?
The production of building materials entails responsiveness to a wide range of individual needs and expectations. From public buildings such as hospitals and schools to manufacturing plants, from homes to shopping centers, each type of building requires its own specific characteristics and standards. While, for example, hygiene is paramount in hospitals, acoustic performance is critical in concert halls. This diversity requires the innovation in our products and the integration of different technologies, encouraging us to continually improve.
However, the construction industry is structured to be quickly affected by economic fluctuations. High interest rates and inflation may specifically slow investments in the industry by increasing production costs, leaving investors exposed to unfavorable scenarios such as increased production costs or difficult access to financing.
At Kastamonu Entegre, we are resilient against such economic fluctuations thanks to the benefits of being a global corporation, our experience in different markets and our flexible production capacity. We are determined to continue to lead the industry through sustainability and innovative solutions.
5) Could you please tell us about the robotic applications in your plant? How did the need to invest in robots appear initially?
Kastamonu Entegre enjoys a corporate culture driven by R&D and innovation. We first invested in robotics in 2005. The supplier we worked with suggested that we use robots to handle the stacking process at the end of the line. By implementing this suggestion, we took an important step towards enhancing efficiency and precision in production.
This initial experience steered our company's approach to automation systems. Since then, we have continued to integrate robotics into our production processes in line with our strategic goals. Today, robots in our plants make our production processes faster and more accurate by performing works in automation areas. These applications help us maintain our global competitiveness and achieve our sustainable production goals.
6) How many robots do you use in total in which production lines and applications?
In 2005, we engaged our first industrial robot in the stacking process at the end of our laminate flooring line. Since then, we have continued to spread the use of robotics in our plants. We currently use 9 robots on laminate flooring production lines and 13 robots on packaging lines, sanding outlets, quality sorting, profile lines, and block insertion/removal in cargo loading units. In total, 22 industrial robots are actively working in our different units. In the coming period, we will continue to strive to increase this number and to further improve our production processes.
7) What kind of feasibility service did you get from your robotic system integrator/robot supplier before investing? How important do you think the integrator selection and working with the right integrator are?
We usually coordinate the process of supplying robots together with our prime contractor. For our production line investments, we evaluate alternatives after deciding that robotics is the most appropriate solution for the processes in question. Our supplier proceeds with the trusted company which previously delivered positive results.
For some applications, we work directly with integrators. In this process, we hold preliminary meetings with the companies and share our objectives and business details. After analyzing the application examples and demo lines, we start working together when we are convinced that all technical and operational processes are well-matched. We believe that choosing the right integrator is critical to the success and efficiency of projects.
8) What were the outcomes and benefits of production? How did investing in robots help you? What would you say about the use and importance of robots? How did investing in robots affect your workforce?
Robotic processes enhance productivity, saving time and space. Compared to traditional methods, industrial robots take up less space, are easier to maintain and considerably reduce costs in the long run. The cumbersome nature and high maintenance costs of the equipment used in old methods are the primary factors driving demand for robotic technology, among others. In addition, the initial cost of robotic investments decreasing with the advance of technology makes these solutions more preferable.
At Kastamonu Entegre, the robots we used in block insertion and removal processes also increased employee satisfaction by reducing the burden on our employees regarding occupational health and safety. The low-maintenance robots simplify these processes, which is a key factor that has a positive impact on overall satisfaction at work. These investments make us more competitive and serve our sustainable production goals.
9) In what areas and for what purpose are you planning to invest in robots in the future?
Our investment in robotics is part of our twin transformation goals. Therefore, we want to maintain and increase our competitiveness on a global scale by rapidly adapting to green and digital transformation processes. We are prepared to make the required investments to reach this goal.
Naturally, we will continue to use and make widespread industrial robots in our current applications. Using robots in different locations of our lines, we also take major actions to carry out various applications performed by traditional methods. In addition, we are prepared to make new investments depending on the outcomes of our actions.
At Kastamonu Entegre, all these investments cater for a need, bringing tangible benefits to our business processes. That is why every step we take includes a plan and a strategic goal. We will continue to invest towards these goals in the future.
10) How do you think artificial intelligence will affect production processes in the medium term?
The role of artificial intelligence in enhancing operational efficiency and reducing costs in the manufacturing industry is beyond dispute. Especially, the integration of robotic process automation and machine learning algorithms makes production lines significantly more efficient. AI robotics applications not only offer powerful transformation in areas such as data analytics, predictive maintenance systems and automated quality control, but also add predictability and flexibility to production processes, thus enabling faster response to customer demands.
At Kastamonu Entegre, we are determined to continue our efforts to integrate AI technologies into our production processes as part of our digital transformation strategies. Our goal is to offer high-quality innovative data-driven products while achieving cost benefits. In addition, we aim to continuously improve our product quality through systems that instantly monitor and optimize the performance of our production lines, manage maintenance processes more effectively and increase agility.
In the coming period, we plan to increase our operational efficiency and reinforce our global competitiveness by further amplifying the integration of artificial intelligence. We will also prioritize training and adaptation programs to ensure that our employees can work in harmony with artificial intelligence technologies.
11) What is your vision for Industry Digital Transformation? Could you please tell us about your successful applications?
Our vision of industry digital transformation relies on the rapid completion of twin transformation process by integrating green and digital transformation. In this respect, digital transformation is one of key strategic priorities at Kastamonu Entegre. We rendered our business processes more efficient and sustainable through considerable investments made in this area recently.
In the past, manually monitoring the performance of production lines was a time-consuming labor-intensive process. Today, all data is captured instantly and can be monitored against various parameters thanks to the digital systems we have installed. The integration of these systems with mobile applications allows us to easily monitor the efficiency of our equipment. In addition, the digital programs we use in our production and maintenance processes enable us to analyze all parameters both immediately and retrospectively, quickly identifying the root causes of potential problems and finding solutions.
The large pool of stored data we have created gives us the means to manage our decision support mechanisms more effectively. Analyzing historical data in our work with suppliers, we can predict quality outcomes in advance. These benefits that digitalization adds to our business processes make us more determined and motivated for transformation. Digital transformation, an integral part of our corporate culture, will continue to change the way we do business.
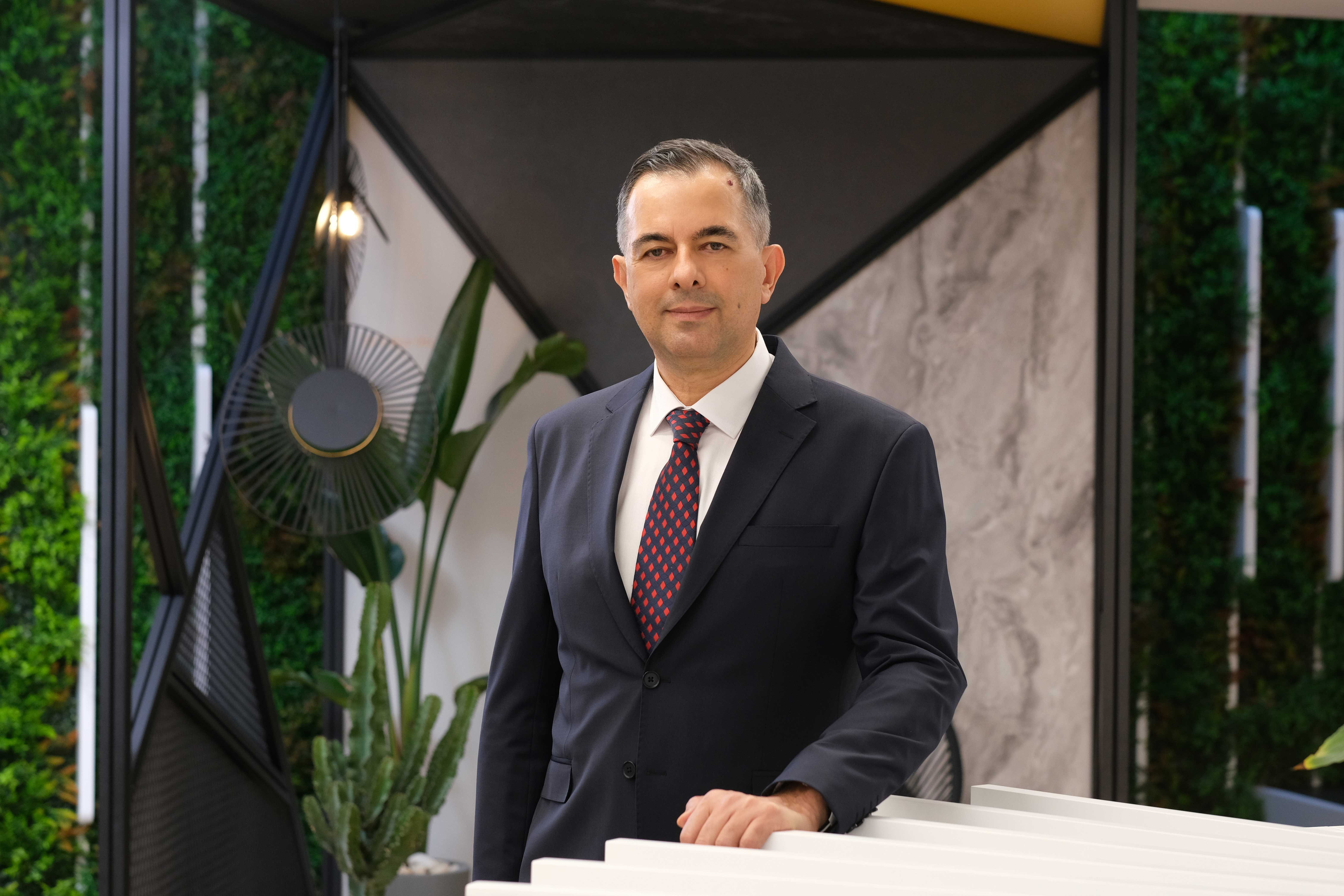