27th Quality Circles Sharing Conference Awards Presented: Two Awards for Kastamonu Entegre
A global brand in the wood-based panel industry, Kastamonu Entegre returned with an award from the 27th Quality Circles Sharing Conference organized by the Turkish Quality Association (KalDer) Ankara Branch. Kastamonu Entegre won two awards in the “Quality Circle” category, increasing the total number of “Quality Circle” awards it has received over its five years of engagement with KalDer to nine.
As one of the world’s largest manufacturers in its industry, Kastamonu Entegre continues to promote the effective implementation of its quality system at every stage of production. The Quality Circles program implemented as part of Total Quality Management enables employees to take initiative in their work areas and overcome issues related to quality, efficiency, ergonomics, and workplace safety through teamwork. Thanks to this program, employees work in a facilitated fashion while contributing to the improvement of work outputs. Brought to life with the engagement of volunteer teams from both domestic and international plants, these projects lay the groundwork for efforts aimed at enhancing product quality and efficiency. The projects stand out as they represent the corporation at the Quality Circles Sharing Conference organized by the Turkish Quality Association (KalDer). Winning two awards in the “Quality Circle” category this year, Kastamonu Entegre has increased the total number of “Quality Circle” awards it has received to nine.
Achievement Through Teamwork
Every year, the KalDer Ankara Branch awards prizes in the Quality Circles and Kaizen categories to encourage teamwork within organizations and promote the sharing of best practices. In this context, Kastamonu Entegre was honored with awards this year for the projects carried out by its teams “Tester Screwdriver” and “Against Time”.
Achievement Coming after Detailed Reviews
The Kastamonu Entegre teams accomplished the detailed evaluation process by excelling not only in the desk review of their projects but also in on-site assessments. Kastamonu Entegre’s efforts in quality management and process improvement were observed during the on-site assessment conducted by the KalDer Ankara team.
The Tester Screwdriver project addressed hydraulic motor failures resulting in production losses and decreased plant capacity utilization. Using occupational health and safety (OHS) analyses to identify risk factors, the project team conducted Brainstorming and Why-Why analyses to determine root causes. The team identified 12 different countermeasures to address the root causes, implemented these measures to improve outcomes, organized training sessions, and updated maintenance plans.
Gebze Tester Screwdriver Team
The Against Time project dealt with a technical issue that negatively affected the production process and caused waste of raw materials and energy. Following the occupational health and safety analyses, the project team aimed to reduce risks to an acceptable level and enhance production efficiency. After conducting Brainstorming and Why-Why analyses to identify root causes, the team defined various types of measures, developed time plans, and implemented countermeasures; failures were reduced to zero and risks were eliminated.
Tarsus Against Time Team
Kastamonu Entegre continues to contribute to sustainable and eco-friendly production processes at its plants in Turkey and abroad while carrying out quality- and innovation-oriented projects to enhance efficiency.
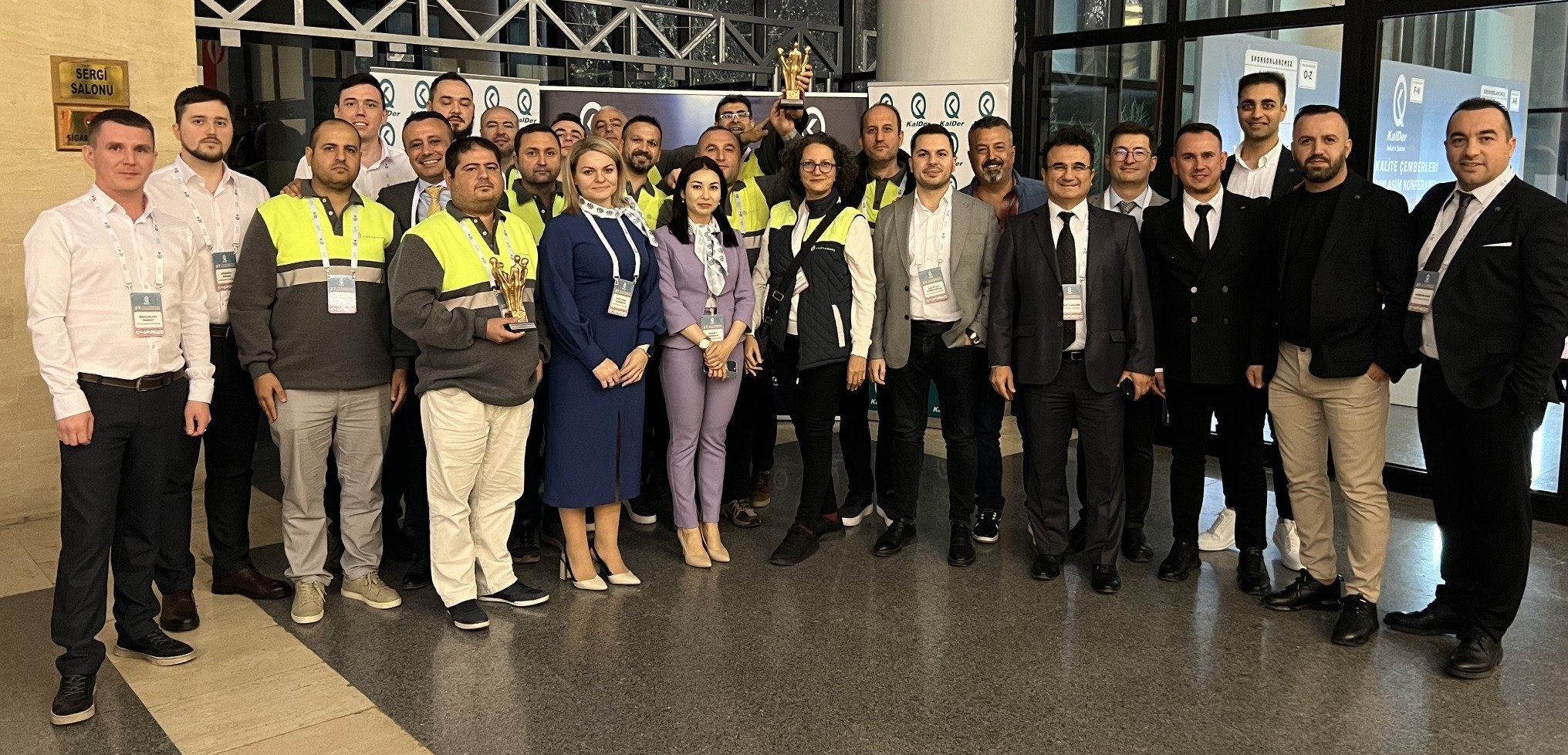