Kastamonu Entegre: Steering the Future Through Sustainability and Innovation
At Kastamonu Entegre, sustainability is not just a responsibility but also an integral part of our business model. In your view, what is the most critical transformation a company must undergo to fully embrace sustainability?
The most crucial transformation for a company to embrace sustainability is to integrate it not as an additional strategy, but as a core principle embedded into every stage of its business processes. Companies should approach sustainability as a long-term commitment, setting concrete goals and developing innovative solutions to achieve them. Businesses that adopt this transformation not only minimize their environmental impact but also gain a competitive edge through innovation.
At Kastamonu Entegre, we embrace this philosophy by focusing on bio-based materials, energy efficiency, and circular solutions, pioneering initiatives that will steer the future of our industry.
PureBoard: A first in Turkiye, a milestone in the industry
PureBoard, one of your latest steps toward circular economy practices, stands out as the first particleboard in Turkiye to be produced entirely with bio-based adhesives. How did the development process of this product take shape? Can we consider PureBoard a turning point for the industry?
As Turkiye’s first particleboard produced entirely with bio-based adhesives, PureBoard represents a milestone in the industry, reflecting Kastamonu Entegre’s vision for environmental sustainability and innovation. This innovative, no formaldehyde added product helps the conservation of natural resources by reducing reliance on fossil resources and plays an active role in combating climate change thanks to its low carbon footprint.
One of PureBoard’s key features is its formaldehyde-free composition, which ensures low emission levels, improves indoor air quality, and promotes healthier living spaces. As the beginning of a new sustainable production standard for the industry, PureBoard paves the way for the widespread adoption of bio-based and low-emission products. Moving forward, we will continue to push the boundaries of sustainable manufacturing.
Sustainability backed by circular economy projects
You are leading pioneering projects in the field of circular economy. You have innovative solutions such as making boards from coffee waste. These projects not only reduce environmental impact but also foster collaborations across different industries. How do you see the economic and ecological benefits of your circular economy projects? Which raw materials do you plan to explore from a new perspective in the future?
We see our circular economy projects not only as an approach that promotes environmental sustainability but also as a transformational model that enhances economic value. Through waste management, the use of bio-based materials, and industrial symbiosis projects, we achieve significant ecological and economic gains. In this field, our team of 21 experts at our R&D center collaborates with public bodies, EU organizations, startups, research institutes, and universities to develop innovative projects.
One such project is our CoffeBoard panels, which, as you mentioned, are produced by upcycling coffee waste. Processing used coffee grounds collected from major beverage chains into high-quality, sustainable panels is a crucial initiative, as it not only fosters collaborations with startups but also raises eco-friendly production standards. Another product, HempBoard, is made using the woody core of the hemp plant as raw material. This innovation substantially contributes to our goals of diversifying raw material sources, reducing waste, and creating new revenue models. Additionally, it gives us further competitive edge by responding to the growing global demand for innovative and sustainable products.
This year, we will expand our 100% recycled production pattern from Italy to our plants in Gebze, Balıkesir, and Romania. With the recycling plants we established in Gebze and Balıkesir, we aim to reintegrate 300,000 tons of wood waste into the economy every year. With a total investment of TRY 160 million, we are committed to increasing the use of recycled materials in particleboard production, promoting sustainable raw material usage, and leading the transition to a circular production model.
Technology and innovation offer a significant opportunity to minimize the environmental impact of production. How do you integrate sustainability with digitalization and AI-driven production patterns? For instance, do you plan to develop solutions that optimize waste management through smart manufacturing systems in the future?
At Kastamonu Entegre, we take firm steps in efficiency, resource conservation, and environmental impact mitigation by integrating digitalization and AI-driven production patterns into our sustainability strategies. Especially, we aim to develop AI solutions for waste management and energy efficiency, enabling us to monitor and optimize our production processes in real time. By taking smart manufacturing systems to a further level, we plan to enhance our operational efficiency and reduce our carbon footprint.
“We prioritize investments in renewable energy”
Kastamonu Entegre’s investments in renewable energy are remarkable. However, energy is not just a production input, it is also a matter of vision. What is your primary motivation behind your investments in renewable energy?
As a company that directly sources 67% of its energy consumption from renewable resources, our biggest motivation in renewable energy investments is seeing energy not just as a production input but as a core element of our long-term sustainability strategy. While we focus on reducing our carbon footprint at every stage of production through innovative energy efficiency solutions, we also develop projects that allow us to utilize renewable resources more effectively. Through our biomass power plants, rooftop solar energy systems, and wind power projects, we take pioneering steps in the global energy transition, working to steer the future of sustainable production.
“Sustainable forest management is one of our top priorities”
Wood-based panel production is an industry that inherently relies on the use of natural resources. The concept of ‘sustainable forest management’ is becoming increasingly important. At Kastamonu Entegre, what are your top priorities in this area? How do you set industry standards for forest management?
Undoubtedly, sustainable forest management is one of our top priorities. In our production processes, we exclusively use wood sourced from regeneration and maintenance operations, strictly avoiding raw materials of unknown origin. By managing sustainable supply chains in our facilities, we ensure the efficient use of forest resources and promote recycling by incorporating by-products of the wood industry into production.
What will be the greatest transformation Kastamonu Entegre aims to achieve in sustainability and innovation? If you could make a radical change in your production processes today, in which area would you want to make the biggest impact?
Our ultimate transformation goal is transitioning to a zero-waste production pattern that is entirely based on renewable resources. We strive to be a pioneering company in the wood-based panel industry by increasing the use of bio-based materials and leading the way in carbon-negative production processes.
If we could implement a radical change today, we would prioritize taking waste management and recycling to the next level, fully embracing a 100% circular economy model in our production. Creating a production ecosystem that maintains the same quality standards with recycled materials while minimizing the use of natural resources would be a game-changer not only for our company but for the entire industry. By blending innovation with sustainability through groundbreaking solutions, we are committed to building the production pattern of the future today and becoming a globally inspiring company.
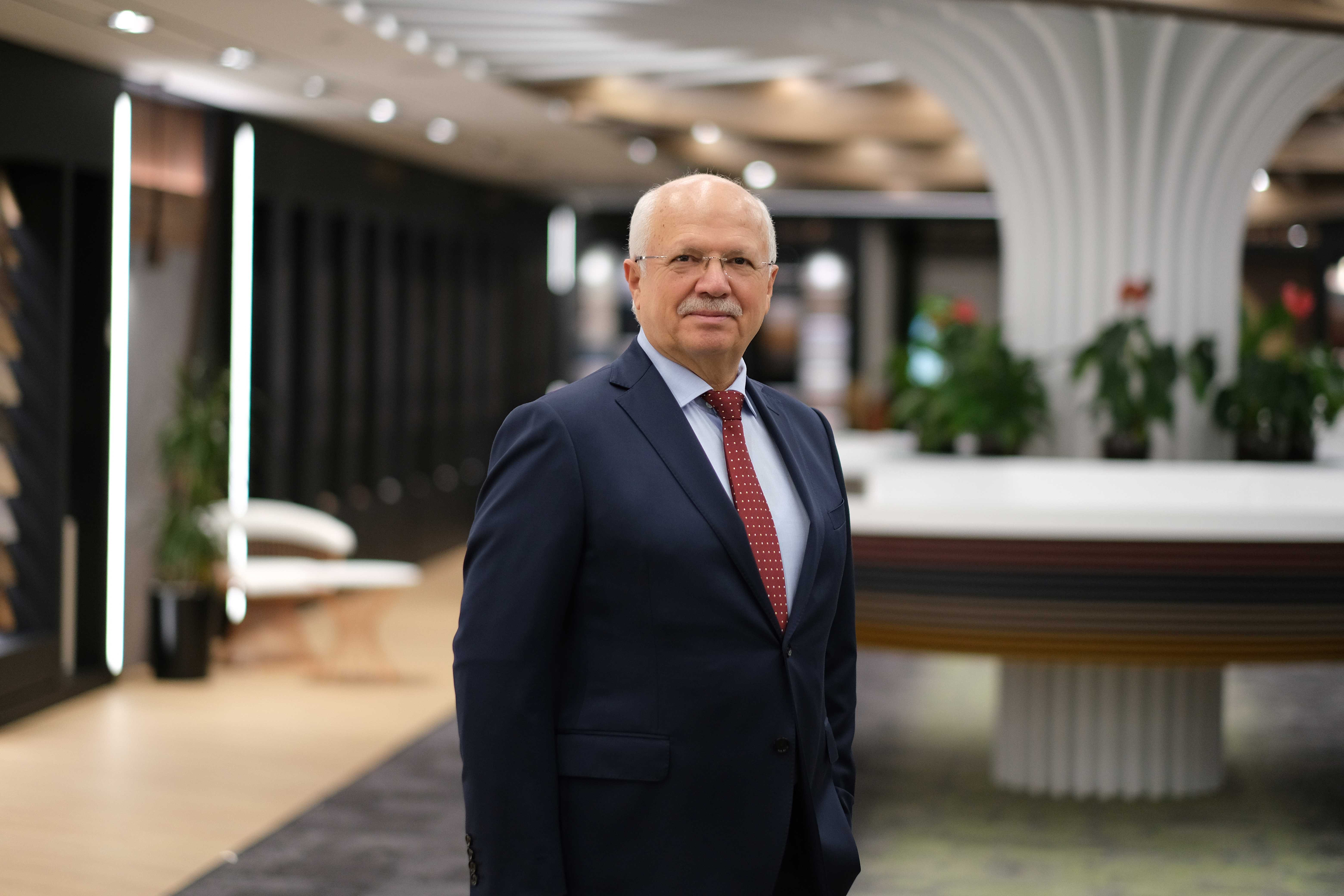